New era of apprenticeships
One of the many things Nina Wronski has learned over the past year-and-a-half is that no two working days are quite the same.
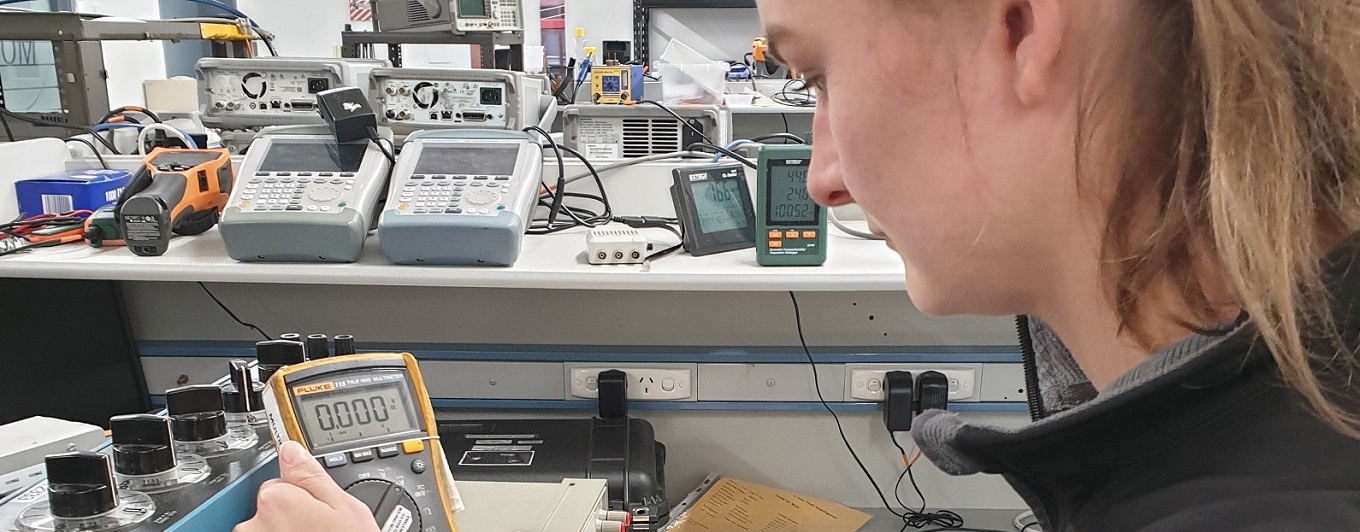
Since becoming MSL’s first apprentice(external link) in June 2019, Nina has balanced working at the national metrology institute, with industry placements and study, including undertaking NZ Diploma in Engineering (Mechanical) papers through WelTec.
“The apprenticeship has been a great experience so far, and I’ve had so many opportunities,” says Nina. “I’ve learned that there’s something in metrology for everyone’s skills, interests and abilities.”
Those opportunities have included work experience in calibration metrology labs at Air NZ and the NZ Police, and undertaking some challenging projects.
“One of these involved connecting a Raspberry Pi (a credit card-sized single board computer) to wireless sensors using Python coding to gain and map data on temperature and humidity. That kind of coding experience is really valued in industry.”
Addressing an industry need
MSL introduced its two-year apprenticeship programme in 2019 in response to a 2017 Royal Society report(external link) about a deficiency in the practical skills of those entering the NZ science technicians workforce.
The report found that many university graduates applying for science technician roles lacked practical skills, and required significant on-the-job training. It also identified that while polytechnics were delivering diploma-level training that was fit-for-purpose for industry, too few were taking this training route.
Among the report’s suggestions was that interested employers provide practical work experience for students during their undergraduate training, lessening the on-the-job training they otherwise have to provide to overcome the deficit of transferable practical skills of new employees.
Further government support of apprenticeships has since come in the form of the Targeted Training and Apprenticeship Fund(external link) (free trades training), which supports learners to undertake vocational education and training without fees.
The commercial context
RF Test Solutions(external link) – a Lower Hutt-based commercial calibration laboratory, which provides electronic measurement services, calibration and repairs – is another playing its part in nurturing the next generation industry professionals.
Managing Director Lex Grubner got his start as an industry cadet, and since founding RF Test Solutions in 2001 has almost always had a young team member undergoing on-the-job training.
“The challenge for us is you can count on one hand the number of other operators in this business in NZ, so being able to employ people with experience is very difficult,” says Lex.
“On the other hand, the reality is that those coming out of university with a degree who say ‘I’m employable’ still have so much to learn. That’s why we have to be prepared to take on people as apprentices.”
Hands-on experience
Shairae Taepa began working at RF Test Solutions in 2019, first on a casual then a part-time basis, while studying for her NZ Diploma in Engineering (Electrical) at WelTec. Now she has completed her qualification, she will work in the business full time.
“I wanted to get an insight into what it would be like to work in industry, so I started doorknocking,” Shairae explains. “I introduced myself at RF Test Solutions, and Lex gave me a tour. As he was showing me around I thought ‘wow! There’s so much I could learn here’.”
In a small business, says Lex, it’s challenging to allocate the time and resources required to develop young talent. Shairae initially worked primarily on administration tasks that required limited supervision, but gave her a broad understanding of the business’ activities; increasingly she’s gained practical lab experience, including doing calibrations and repairs.
Nina and Shairae, who recently spent a day in each other’s workplaces to further their exposure to different industry opportunities, also both note a culture among experienced technicians to mentor and support those new to the industry.
“As a young person coming into metrology you get a lot of support from your fellow workers,” says Nina. “Most of them tell you that when they started working in the lab they had a lot to learn, so they understand where you’re coming from and are willing to give you a hand.”